In 2020, we made many deals about organic fertilizer equipment. At the beginning of 2021, we summarized the top sell machines used for producing organic fertilizer in SX. The following is detailed information.
-
Solid-liquid separating machine
Making organic fertilizer, the materials always be all kinds of poultry manures and animal waste. As we know, manures always have high moisture content, which makes them poor air permeability. Then the manure management process may be also inefficient. To solve this problem, we designed two kinds of poultry manure dewatering machine: screw extruding type and inclined screening type.
According to the statistics, cow dung dewatering machine and chicken manure dehydrator is the most popular tow models in SX. With excellent performance and stable efficiency, our solid-liquid separator becomes the first choice for many customers.
- Groove type composting equipment
Composting is the most important process in a complete organic fertilizer producing factory. It’s the guarantee of the fertilizer products quality. In all our fertilizer composting machines, the groove type may be the most economical one. No matter which scale your fertilizer plant is, a groove type compost turner can work efficiently. For large scale composting need, you just need to build more composting grooves.
Adopts aerobic composting method, our groove compost turner can crush and mix the fertilizer materials evenly. In just about 15 days, the composting of manures can be finished efficiently.
- Rotary drum granulator
After composting, manures will become powdery forms. Generally, you can pack the composting fertilizer for self using or selling. But most people choose to make the fertilizer powders into granules. That’s because granular fertilizers may have more stable structure and fertility, the transportation can be more easily.
As for organic fertilizer granulator, rotary drum pelletizer is the best selling one. Adopts wet granulating process, fertilizer materials can agglomerate into fine granules because of the centrifugal force produced by high speed rotating drum.
Moreover, drum granulator also can be used for making compound fertilizer, choosing it, you can really get high profits with low cost.
Roller extruding granulator is also known as double roller extrusion granulator. It’s mainly used for making compound fertilizer pellets by the extruding of two fertilizer roller sheets. With reasonable design and structure, our roller extrusion granulator is always the best sell dry powder fertilizer pelletizer. So how to use the granulator efficiently? 5 steps of roller extruding granulator fertilizer making process are as follows:
1.Add qualified fertilizer materials into the fertilizer mixing machine and mix them evenly. Before this procedure, you can use a fertilizer batching machine to make sure the proportion of each fertilizer material. In SX, we have automatic dynamic fertilizer batching machine widely used in continuous compound fertilizer making process.
2.Feed fertilizer materials into the roller extrusion granulator by disc fertilizer feeding machine. The mixed material is added into the gap between two opposite rotating roller shafts through a vertical screw feeder. During the extrusion process, the pressure of the material increases gradually. When the gap between the two shafts is relatively small, the pressure of the material is relatively large, and then gradually decreases. In the extrusion process, the apparent density of the mixture can be increased by 1.5-3 times due to the decrease of the empty volXume of the material.
3.After granulating, conveying the fertilizer pellets into rotary screening machine. Small fertilizer particles can be returned into the disc fertilizer mixer. And large fertilizer particles can be crushed into small size by fertilizer crushing machine, then convey them into the feeding machine.
4.After crushing, the unqualified materials can fed into the roller granulating machine and granulated again. During this process, the utilization of fertilizer materials can be greatly improved.
5.At last, you can pack the final fertilizer pellets into bags by automatic fertilizer packing scale. Then storing and loading of fertilizer will be much more convenient.
Composting process is the degrading and stabilizing of organic materials by microorganisms under the appropriate moisture content, oxygen concentration and other conditions, so as to achieve the purpose of killing parasite eggs and harmful microorganisms. The composted material won’t contain pathogenic bacteria and weed seeds, so it’s suitable for application in soil to bring crops higher nutrition content.
Composting process generally includes fermentation, turning and aeration. As a recommendation, the groove type aerobic composting has distribution system, overturning system and aeration system:
1. Groove type composting machine: to meet the requirements of moisture and pH in material fermentation, some microbial bacteria needs to be added. The turning machine can give full play to its stirring function, improve the permeability of raw materials, absorb a lot of air at the same time, and increase the temperature of the compost pile. If the temperature is too high, it can absorb fresh air again, so that the temperature will drop again.
2. Distribution truck: it can evenly distribute the materials in the composting groove, so that the forklift doesn’t have to go in and out of the grooves frequently. It greatly reduces the transfer cost of raw materials and improve the work efficiency.
3. Moving crane: each groove aerobic composting system is generally composed of 8-10 composting grooves, but generally only need one compost turner. In order to save investment, it’s necessary to switch the position of turning machine between different composting grooves, and the moving crane plays a good role.
4. Aeration system. The function of aeration system is to ventilate and oxygenate the fertilizer materials in grooves, so that the microorganisms in the materials can interact with oxygen, and then the materials can be fully composted to produce valuable humus. It also greatly shortens composting time.
There are two ways of feeding and discharging when using groove type compost turner: batch and overall feeding and discharging. The characteristics of batch feeding and discharging are feeding at the front end of the composting groove each time, and the material is moved to the other end by working turning machine. The second feeding starts again and again until finish the whole manure composting process. The overall feeding and discharging characteristics are that the whole fermentation tank is full at one time, and when the fermentation cycle is over, the materials are discharged in batches.
Characteristics of groove type turner:
1.The composting width can be 2-6m. The whole composting process only costs 7-10 days and it can compost about 80-360 cubic meters of fertilizer materials per hour.
2. The innovation of the machine is to make use of the deep pool design of underground space and the new technology of long-distance turning, and make use of the limited land area to realize the large-scale treatment of organic waste.
3. The unique pool type continuous aerobic fermentation technology is adopted to make the organic wastes quickly decomposed, dewatered, sterilized and deodorized, so as to achieve the goal of harmless and resource-based treatment.
Requirement of building composting groove for groove type composting machine:
The composting grooves need to be reinforced concrete structure. Two adjacent grooves share the same groove wall, and the width of the wall is determined according to the requirements of the turning machine. The groove wall should be able to bear the pressure of turner, and the bottom plate of composting groove should not only bear the gravity of fertilizer materials, but also bear the gravity of loader, and meet the requirements of ventilation.
1. Adjustment of material moisture: the moisture content of composted animal manure should be adjusted to 40-65%. Low moisture content may cause slow fermenting; high moisture content makes poor ventilation. Therefore, if the manures moisture content is too high, you can add some mushroom residue, straw and sawdust. All you can choose our manure dewatering machine to save time and energy.
2. Ventilation process. In the aerobic composting process of poultry waste, oxygen supply measures should be increased in the operation process. According to the need, the oxygen supply can be flipped or forced by tools.
3. Working of organic fertilizer turner. In general, after 48 hours of raw material stacking, the material temperature will rise to 50-60 ℃ and above 65 ℃ after 72 hours. Usually, the fermentation process will appear 2-4 times of high temperature above 65 ℃, and the fermentation can be completed by turning over 2-4 times. The fermented material was dark brown, and the temperature began to drop after fermentation. When the temperature dropped to room temperature, the fermentation was completed.
4. Aerobic fermentation cycle control. Under suitable temperature and moisture, the whole fermentation process can be completed in 7-15 days. This process can realize deodorization, insecticidal sterilization and fermentation.
Except for the above matters, in the process of organic fertilizer production, we need to pay attention to the chloride ion content. Some fertilizers contain a lot of chloride ions, and some manufacturers use ammonium chloride to add to organic fertilizer to increase the nitrogen in total nutrients. But too high chloride ion content will affect the growth of crops.
For the drying equipment of organic fertilizer production line, firing temperature is very important, which directly affects the drying quality. So it is very important to control the firing temperature strictly. But the firing temperature will always change, so how to control the temperature of the fertilizer drying machine?
1. If the firing temperature becomes low, the feeding amount of the dryer should be adjusted to reduce the material. When the firing temperature becomes higher and the feed rate is at a higher level, the coal should be reduced first instead of feeding fertilizer materials.
2. Eliminate the height potential energy difference of dryer. This is the main reason of dust spilling. The elimination of height potential energy difference is caused by powder drop of hopper, protective cover and chute of handling equipment. We should try our best to reduce the fall and the inclination angle of the chute. Some airtight chambers are better to cause negative pressure, which is conducive to the collection of dust.
3. Sealing control of dryer. It can be partially sealed, integrally sealed or closed chamber, etc., and the dust producing point can be sealed with a sealing cover, which can greatly reduce the material scattering and dust.
4. The transportation equipment with good sealing performance shall be used to reduce the height difference and inclination angle of discharge material flow, and the flow separation facilities shall be set as far as possible. It can not only enhance the configuration flexibility and efficiency of each operation room, but also reduce the scattering and dust.
5. Use the exhaust system. In order not to let the dust bring more pollution, we can also remove the indoor dust through the exhaust system, that is to remove the indoor exhaust gas.
1. In the composting process of organic fertilizer making plant, the materials should be crushed. The composting of organic fertilizer needs to be fully turned over. Some raw materials may don’t have suitable particle size, which will affect the composting efficiency. So it is not conducive to the mixing and composting of materials without crushing.
2. In the process of powder fertilizer processing, organic fertilizer crusher is necessary. After the second fermenting of composted fertilizer materials, some materials may cake or stick together, which would reduce the fertilizer quality.
- There was a need to control the particle size of organic fertilizer in agricultural machinery fertilization, otherwise large-size organic fertilizer is easy to cause uneven fertilization, so it is necessary to use the organic fertilizer crusher to crush the particle size in the processing of powdery organic fertilizer.
- The powdered organic fertilizer crushed to 5mm is more conducive to pack. Moreover, too large fertilizer size is easy to cause uneven transportation, even blocking, so it also needs organic fertilizer crusher.
3. In the process of granular organic fertilizer, organic fertilizer crusher is also essential.
- Granular fertilizer is usually produced by extrusion or agglomeration. Whether extruding or agglomerating, the size of powdered organic fertilizer should be controlled at 50 mesh, so that the granulation effect will be ideal. Therefore, the size of 1-5mm powder fertilizer needs to be processed by crushing equipment.
- In order to increase the hardness of organic fertilizer particles, it is necessary to crush the organic fertilizer raw materials. Organic fertilizer is a kind of organic material with very small density. In order to enhance its density and achieve the reasonable degree, the powder fertilizer needs to be small enough, which is the requirement of 50 mesh.
Due to the hole diameter, cylinder length and process requirements of organic fertilizer drum dryer, the welding method is selected during installation. It is the best way to install the dryer, but if you can’t master the key points and welding quality in the welding process, it will seriously affect the drying effect. In order to ensure the welding quality does not affect the machine performance, the welding quality should be paid attention to. In the welding process, we must grasp the three quality factors of welding:
- Remove welding residues in time. The sealing of the machine directly affects the drying efficiency and energy consumption. If the welding is not good, because of high temperature and high pressure, the equipment is easy to cause corrosion cracking and seal falling off, so the welding parts need to be removed.
- After welding, the cleaning work should be done to avoid impurities affecting the performance of the machine and even causing damage to the machine.In fact, besides fertilizer drying equipment, timely cleaning after working is very important to every fertilizer making machine.
- Conduct professional welding inspection. Repair shouldn’t be more than two times after installation, so the machine after welding must pass the bending test and tensile strength test, so as to ensure that the machine can be put into production.
Belt conveyor is the necessary equipment in a complete fertilizer making factory. It can make sure the whole plant work smoothly and is the basis of high efficiency. So the maintenance of fertilizer conveying machine is very important. So what things need to be considered when using fertilizer conveying machine?
1.The belt should be kept clean during use and storage, avoid direct sunlight or rain and snow, prevent contact with acid, alkali, oil, organic solvent and other substances, and be one meter away from the heating device.
2.The warehouse temperature should be kept between 18-40 ℃ and the relative humidity should be kept between 50-80 ℃. During the storage period, the conveyor belt must be placed in rolls instead of folded.
3.Different types, specifications and layers of conveyor belts should not be connected together, and the fixed unloading device should be used at low speed.
4. The feeding direction should be along the running direction of the conveyor belt. In order to reduce the impact of material falling on the conveyor belt. The distance between idlers should be shortened and buffer idlers should be used in the receiving section of conveyor belt.
5. The running speed of rubber conveyor belt shall not be greater than 5 m/s. When transporting large block size and high wear resistance materials, the conveying should be at low speed. If the speed exceeds the specified speed, the service life of the belt will be affected;
6. Attention should be paid to the following matters during the use of conveyor belt:
- Avoid the idler being covered by materials, resulting in inflexible rotation, prevent material leakage stuck between the drum and the belt, pay attention to the lubrication of the moving part, but do not grease the conveyor belt;
- Before turning on the machine, it’s necessary to make sure there is nothing on the conveying belt;
- If the conveyor belt deviates or broke, the operator need to repair it in time;
- The conveyor belt shall be prevented from being blocked by the frame, pillar or block material to prevent breakage and tearing.
A complete organic fertilizer making plant contains composting, mixing, crushing, granulating, drying and other process. From the surface, since the particles are formed, is it not necessary to dry them? In fact, the drying of granular products is very important. So why do we need to dry the fertilizers after granulation?
1.Reduce the moisture content of granular organic fertilizer
As we all know, the moisture content of organic fertilizer raw materials is relatively high. Although the moisture content of materials has been reduced during a series of processes, the moisture content of final products is between 20% and 40% according to the characteristics of the materials. In order to prevent fertilizer products from sticking, drying is necessary.
2.Increase the strength of organic fertilizer pellets
In the process of making commercial organic fertilizer, low strength granules are disadvantageous to commercial packaging and transportation. In the process of transportation, low strength fertilizer granules may increase the damage rate of particles. Therefore, to meet the needs of high economical profits, a fertilizer drying machine is necessary for organic fertilizer producing.
3.Extend the storage life of fertilizer pellets
After making organic fertilizer materials into granules, it takes time from packaging to application, which requires the long preservation of organic fertilizer without reducing the nutrients of fertilizer. The loss of nutrients is often due to volatilization and particle strength reduction, so drying can effectively extend the storage and transportation period of granules.
From the above information, it’s easy to know that after granulating, using a fertilizer drying machine can reduce pellets damage, moisture content and efficiently prolong the pellets storage life. Therefore, a drying machine is very important to a complete fertilizer making line.
Organic fertilizer and compound fertilizer are common used fertilizers in farms. They have different functions to plants and crops. In fact, blending different fertilizers can bring crops higher yields. No matter you are a fertilizer manufacturer or farm owner, making blending fertilizer can also bring you wonderful profits. So what are the advantages of blending fertilizer?
- Compound fertilizer has high nutrient contents, fast fertilizer effect. But the duration of fertilizer effect is short, and its fertility is very simple. But organic fertilizer is just the opposite. So blending organic fertilizer with compound fertilizer can complement each other perfectly and meet the needs of plant growth for nutrients.
- Using compound fertilizer, some nutrients may be absorbed by soil and cause soil hardening. But mixing it with organic fertilizer together can reduce the association surface between compound fertilizer and soil, reduce the probability of compound fertilizer being fixed by soil, and enhance the availability of fertilizer nutrients.
- Generally, compound fertilizerhas high solubility, which will cause high osmotic pressure to the soil after utilization. That is not conducive to the absorption of nutrients and water by crops, and increase the chance of nutrient loss. If making blending fertilizer from compound fertilizer and organic fertilizer, the problem can be solved perfectly, which is conducive to the absorption of nutrients and water by plants.
Except for making organic and compound blending fertilizer, there are also many other blending fertilizer making projects. As a professional fertilizer machine supplier, we can provide you complete fertilizer making layouts and economical equipment.
As the basis of making high efficiency organic fertilizer, composting is also the most important process to manage organic fertilizer materials. To save the cost of buying turning machine, many people choose used or second hand fertilizer compost turner. Its price is truly lower than new composting equipment. But in fact, the used fertilizer turning machine is not recommended. The reasons are as follows.
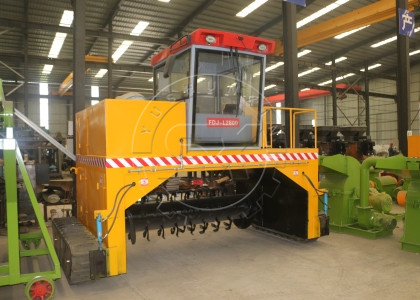
Crawler Type Organic Fertilizer Compost Turner
1. Performance
It’s obvious that the performance of used compost turner is not good as new turning machine. Old turning machine must have been working for long times, no matter the wearing parts or core parts, they must have different degrees of wear and tear. Ageing machine parts makes the machine unstable capacity and higher energy consumption, the final composting fertilizer may also don’t have high quality.
On the contrary, a new turning machine with high performance parts have stable structure and excellent capacity, in addition, it costs low energy.
2. Maintenance cost
With old equipment parts, the maintenance of used composting machine may cost you a lot of time and money. If you don’t know much about mechanics, buying a used fertilizer turner is really not a wise choice.
As for SX organic fertilizer compost turning machine, we use the most quality materials for machines. Such as the groove type compost turner, the composting teeth can work at least one year. Choosing it, you won’t be bothered by high frequency maintenance. Even if the machine broken, with reasonable structure, you can maintain it easily. If you don’t know how to repair, we can provide you free maintenance guidance.
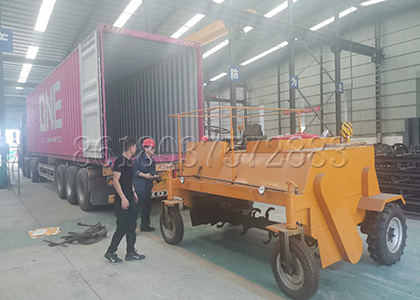
moving type compost turner delivery
3. Warranty
Most used turning machines are sold by privately, which means you won’t get quality assurance. Once you paid for the machine, the seller won’t provide you after-sale service. Even if there is a problem with the machine, you can only solve it by yourself.
But if you choosing a formal fertilizer turning machine supplier, these problems will not exist. With more than 15 years business experience, SX always can provide you high quality fertilizer machines with low cost. Most importantly, we provide you one year warranty. In the year after you received our fertilizer making machine, if the machine has any quality problem, we can provide you maintenance service.
Nowadays, more and more people are making organic fertilizers. And the most common way people choose is to make organic materials into pellets.
Want to make organic fertilizer granules, the selection of granulating machine is very important. At present, people always choose rotary drum granulating machine and pan type granulator. These two granulators always are used for large scale organic fertilizer wet granulating factory. So if you want a small capacity organic fertilizer granulating factory, how to make fertilizer balls economically?
Besides large size organic fertilizer granulator, we also have special granulating machine used for making small quantity dry fertilizer pellets: dry flat die granulating equipment. Adopts dry extruding granulating method, pellets produced by this granulator don’t need to dry. You can pack them directly, which can save you the cost of drying machine.
The fertilizer pellets are cylindrical with diameter about 3-8mm. So if you want to get fertilizer balls, we have the polishing machine. Fertilizer polishing equipment is an auxiliary machine used with fertilizer granulators. It can bring fertilizer pellets more uniform and round appearance. For small scale organic fertilizer line, connect flat die granulator with polishing machine, you will get round fertilizer balls more economically than using other granulator.
If you want to make large scale organic fertilizer balls by this way, you just need to buy more flat die granulators, and we can design reasonable layout for you.
Rotary drum granulator is an important machine in compound fertilizer making factories, which is used for large scale fertilizer materials granulating. Besides compound fertilizer granulating, it also can be used for organic fertilizer manufacturing line. But we learned some customers found the problem of high temperature of the gearing. That may affect the performance of the whole machine. So what are the reasons? And how to solve this problem?
At first, the lubricating oil is insufficient. The lack of lubricating oil will lead to the increase of friction between bearing and the machine, which will cause excessive temperature. So adding enough lubricating oil before using the granulator is very important.
Secondly, if the lubricating oil is not clean, the bearing will be affected by dust. With the increasing dust, the gearing becomes rough. So the temperature of the gearing will rise continuously and burn down. If the fertilizer making environment is nor clean, this problem will be more serious. So the cleaning of the bearing and factory environment is very important.
Thirdly is the damage caused by long-term use. If the granulator is used for a long time, the parts may be aged, and the damage is inevitable. So when the parts are damaged, it’s better to replace them in time. That not only can prolong the granulator working life, but also can make sure the high performance to bring you wonderful profits.
The last reason may be unreasonable installation. Under normal conditions, the bearing is on the center line of the granulator. If you install the machine by mistake, the bearing temperature rising is obviously. To help you make fertilizer efficiently, we can provide you free installation guidance. If the problem can’t be solved, we can also arrange our technician to your site.
Rotary drum granulator is the most typical large scale wet granulating machine. So the fertilizer producing factories with rotary granulator always has excellent capacity. If you want to build a large scale fertilizer making factory, the drum granulator fertilizer producing plant is really suitable.
This kind of fertilizer making process not only can be used for making organic fertilizers, but also is suitable for compound fertilizer manufacturing. For making organic fertilizer granules, the whole plant consists of manure dewatering machine, large size composting machine, rotary pelletizer, fertilizer drying equipment and granules packing machine.
As for rotary drum granulator compound fertilizer factory, you don’t need to buy the composting machine. But the crushing equipment may be helpful. It can crush the raw materials into small particles, which makes the granulating process more smooth.
All the machines in our rotary granulator fertilizer making plant is made by high performance parts and hard metal materials. Low cost on maintaining makes the whole plant more efficient and bring you higher economical profits. By wet granulating method, the final fertilizer granules have round performance and fine structure. If you want to get more beautiful fertilizer balls, we can equip you polishing machine, rotary screening machine or coating machine. If you don’t know how to make reasonable layout, we can provide you free layout and installing guidance.
Sheep manure is one of efficient hot fertilizer. It contains about 24%-27% organic nutrients. By composting the mixed sheep manure and fermenting bacteria, you can get efficient sheep manure organic fertilizer. So what are the detailed processes of making sheep manure compost?
The first is mixing sheep manure with straw powders(straw crusher can be used for make straws into small particles). The addition amount of straw powders depends on the sheep manure moisture content. The suitable moisture content when composting is about 45%. Then spray bacterial fluid to the manures and mixed them evenly based on the proportion of 1 ton sheep manure mixed with 3kg compound bacteria liquid. In this process, you can add some corn flour to bring bacteria sugar content. It can make the most of fermenting bacteria. After doing these things, mixing the materials evenly by organic fertilizer mixing machine.
After mixing sheep manure with auxiliary materials, you can pile up them into long manure windrows with width about 2-3m, height about 1-2m. Then using fertilizer composting machine once every 3 days to compost the sheep manure windrows. Generally, at the third day after composting, the temperature of manure windrow can reach to 60-80℃. The pest eggs, grass seeds and other useless materials can be greatly eliminated. At the fifth day, the bad smell of poops will disappear. At the ninth day, the composting fertilizer becomes loose and dry. At the fifteenth day, the bacteria manure can be totally decomposed.
The decomposed sheep manure is fluffy, dark brown and doesn’t smell bad. It can be used for fruits, vegetables and all kinds of cash crops.
Bulk blending fertilizer is a new efficient fertilizer widely used for crops. In fact, you can consider it as the combination of different kinds of fertilizers. The largest highlight of BB fertilize is that you can adjust the proportion of different fertilizers according to your soil conditions. So it gradually becomes more and more popular.
For fertilizer making factories, making blending fertilizer is really an economical project. At first, the main process of bulk blending fertilizer production line is just batching and mixing. In SX, we have static and dynamic automatic fertilizer batching machine. With precise batching scale and high automatic degree, they can make high accuracy of blending fertilizer batching. Then you can choose our BB fertilizer mixer for mixing the fertilizer materials evenly. With these machines, you can get high quality bulk blending fertilizer with low cost.
Then, you have many choices to make bulk fertilizer. Such as powdery forms and granular forms, organic and compound blending fertilizer, different compound blending fertilizer and the most common NPK fertilizer. No matter which you want to produce, you will always get excellent profits. With our equipment and free reasonable layout, your whole factory will run smoothly.
Pig manure is a kind of high efficiency organic fertilizer materials. Making pig manure fertilizer, the composting is very important. As the most helpful way, aerobic composting is widely used way to make quality composting fertilizer. So how to make aerobic pig manure composting?
Aerobic composting process refers to the animal manures contact large amount oxygen when fermenting. By this way, the bad smells and useless materials of the organic fertilizer materials can be greatly eliminated. As for the pig manure, you can reduce its moisture content in advance. When composting, you can make them into long windows or build composting grooves. Then choosing suitable composting equipment. As a professional fertilizer machine supplier, we have different kind of organic fertilizer composting machines.
For large scale pig manure composting, we have wheel type compost turner. If you want to make fast composting, the fermentation pot can be really efficient. For medium and small capacity pig poops composting, we have groove type compost turner and windrow turners. No matter which one you need, we can provide you considerate service and technical guidance. Using our aerobic composting machines, your composting process only takes 7-14 days.
-
Uneven fertilizer granules size
Reason: Uneven raw materials moisture content. Pan granulating machine makes fertilizer balls by the adhesion between materials. Moisture requirements of raw materials are about 50%. Higher moisture may cause overlarge fertilizer balls, and lower moisture makes it hard to granulate. So if the moisture content of fertilizer materials are uneven, the final fertilizer balls may can’t have even size.
Solution: add water to the fertilizer materials evenly. To save your time and energy, we equip spray system for the pan granulator. It can spray water to the materials, greatly improve the granulating rate of pan granulator.
-
Hard to make materials into granules
Reason 1: Too large installation angle of the granulating pan.
Solution: the suitable installation angle of the disc is about 35-55°. Smaller angle, larger fertilizer granules; larger angle, smaller pellets. So you just need to adjust the installation angle.
Reason 2: Unsuitable fertilizer material particles
Solution: too large or uneven fertilizer material particles may affect the granulating process. To solve this problem, you can choose our crushing machine to make the fertilizer materials into even size.
1. Disk Type Granulator
The disc granulator is composed of inclined pelletizing disc, driving device, feeding pipe, material liquid sprayer, scraping plate, etc. Due to the small investment and low operation cost of the disc granulator, it is widely used in organic fertilizer production factories.
It is mainly used for rolling pellet granulation with good cohesiveness and powder homogeneous logistics; for fermentation materials with more crude fiber raw materials, it is recommended to crush twice, otherwise, the granulation quality will be directly affected.
2. Stirring Tooth Granulator
It’s a new type fertilizer granulating machine, also known as wet granulation machine. The equipment uses the mechanical stirring force of high speed rotation and the air power generated thereby, so that the fine powder can be mixed, pelletized and dense in the machine, so as to achieve the purpose of granulation. The shape of particles is spherical, particles size can be adjusted by the mixing amount of materials and spindle speed. Generally, the lower the mixing quantity, the higher the speed, the smaller the particles. Stirring teeth granulating has high granulating rate, and the spherical particles have no sharp angle after granulating, and the pulverization rate is low, which is easier to meet the requirements of large capacity production.
3. Extruding Granulator
We have two kinds of extruding granulators: Roller extrusion grnaulator and Flat die granulator. The first one is suitable for making compound fertilizer by the extruding of two roller sheets. And the flat die grnaulator is suitable for making organic fertilizer granules. By the extruding between roller sheet and mold, the pellets always are cylindrical.
Drying process is a very important part in a complete organic fertilizer making factory. Dry fertilizer products have better structure and more stable fertility, and the quality of fertilizer is also very important for you to get more profits. So what are the ways to dry organic fertilizers?
- Dewatering by specific equipment. For organic fertilizer raw materials such as poultry manures, they always have high moisture content. Before making organic fertilizer, you can choose our solid-liquid separator machine. By centrifugation, sedimentation or extrusion, the manure moisture content can be reduced to about 50%. Then you can make them into composting organic fertilizer.
- Drying by heat. We designed a kind of rotary drum drying machine. It’s suitable for drying fertilizer materials or products by heating in a short time. You can choose to make dry fertilizer pellets directly or dry the finished organic fertilizer products for bringing them more stable structure. No matter which way you choose, the final organic fertilizer pellets will have excellent quality.
- Chemical dehumidification. This way can greatly help the organic fertilizer pellets keep dry. You just need to put some desiccant into the fertilizer bags. They can absorb excessive moisture.
As we all know, some materials such as poultry manures, filter mud and mushrooms, can’t be directly used for making organic fertilizer. But composting can give these materials good treatment such as eliminating the pest eggs and grass weeds, reducing moisture content and so on. So why the compost tuner is needed to compost organic fertilizer materials?
People always make composting fertilizer by naturally fermenting. The whole fermenting process always spends very long time even months and it’s very easy to be influenced by weather and temperature. That will badly influence the whole process of making organic fertilizer.
For making fast composting of the organic fertilizer materials and not damage their nutrient, composting equipment is designed. When composting, you can pile the materials into long windrows or composting grooves. Making them naturally fermenting about 3 days. When the temperature of the piles up to 60-70℃, you can choose a windrow composting machine or groove type compost turner to make them fermenting more efficiently(If the composting machine is not used in time, the materials temperature may rise constantly, which will destroy the nitrogen in the materials.).
Organic fertilizer composting machine can evenly mix and crush the fertilizer materials, making great conditions of aerobic fermentation, also reducing the temperature and moisture of the raw materials. The whole composting process only needs about 15 days. If in summer, the process may be much shorter.
Packing makes the transportation and storage of fertilizer products much more easily. But different form fertilizers need different packing machine. So what things you need to consider when choosing a fertilizer packing machine?
- Shape of the fertilizer materials
Granular fertilizers are formed by granulating machines, their shapes are more smooth. Packing fertilizer balls is not very complicated.
Powder fertilizer is directly crushed powdery material by fertilizer crushing equipment, regardless of the original state of the material. If the dust is very large, you can choose the closed bucket elevator.
- The flowability of materials
Because of the roundness and good fluidity of granular materials, they can be packed by automatic packing scale. And you can change the diameter of the three-stage feeding device to adjust the flow rate and control the packaging speed and accuracy.
Powdery materials always have bad fluidity, but it does not need to consider the original state, the spiral feeding mode and forced blanking method can be adopted to realize the material measurement.
- Dust of materials
The proportion of particulate matter is relatively large, and it is not easy to form dust in the air. Therefore, we generally do not need to consider the treatment of dust in packaging. The open weighing method does not pollute the air and factory environment very much.
The proportion of powder material is very light, and there is a lot of dust when packaging. To reduce air pollution and improve the efficiency of the packing machine, it’s better to equip an automatic dust collecting machine for the whole fertilizer making plant.
Set up an organic fertilizer making plant is not a easy project. A reasonable organic fertilizer plant layout can bring you quality fertilizer products and wonderful profits. The first thing to select a suitable organic fertilizer production line is to know the process of making organic fertilizer. The main process of making organic fertilizer is composting, crushing, granulating, drying and packing. More detailed process contains mixing, cooling, screening, coating and so on.
The selection of organic fertilizer producing line always depends on the raw materials. For example, in the crushing process, according to the water content of the raw materials, the selection of the fertilizer crushing machine is also different. For high moisture content materials, you can choose a semi-wet fertilizer crushing machine. For dry fertilizer materials, such as dry cow manure, dry chicken dung, the vertical crusher will be very efficient.
When granulating, the choosing of fertilizer granulator depends on the fiber size of the raw materials. The finer fibers such as chicken manure and pig dung are usually granulated by disc grnaulator or rotating drum granulator; raw materials of crude fiber like cow manure and horse manure are suitable for flat extrusion granulator.
In the drying process, if the budget is sufficient, we often recommend customers to install a cooling machine with the drying equipment. It’s mainly to prevent agglomeration caused by overheating of particles. After granulating, you can also choose coating machine or polishing machine to make the fertilizer granules more beautiful and uniform.
Composting is an important process when making organic fertilizer. So what things need to be focused on?
1. Requirements for the composting raw materials:
It is better to choose fresh poultry manure. The nutrients are not damaged, and the final organic fertilizer products quality can be much better.
2. Requirements for auxiliary materials:
The auxiliary materials(sawdust, straw, etc.) should have suitable moisture content, strong water absorption, suitable particles or length. The addition amount should be determined according to the water content of composting materials. If you don’t know how to make the auxiliary materials into suitable size, our straw crushing machine can be your choice.
3. The strain should be spread evenly:
One ton of organic fertilizer fermentation bacteria needs at least 50 grams of raw materials. If it can not be evenly dispersed on the fermentation materials, you can first sprinkle 50g of bacteria into any of the raw materials such as 500 grams of wheat bran, sawdust, rice bran, etc., and then spread them into the composting materials to make organic fertilizer. You can also use a fertilizer mixing machine to mix them evenly.
4. The moisture content of materials:
The raw materials moisture content should be about 50%. You can add some sawdust or straws to the materials to adjust the moisture content. Another efficient way is using dewatering machine. It can separate the water and organic materials quickly.
5. Requirement of fertilizer windrows:
Using windrow fertilizer composting machine, the width of windrow material is not less than 1.5 meters, and the height is not less than 1 meter, the length can be adjusted according to your capacity requirement.
SX wheel type compost turner is suitable for making large scale poultry manure composting fertilizer. It’s also our best-selling large composting equipment. So why it has good reputation in composting machines? The following may be the reasons:
1.Excellent capacity:
Our wheel type compost turner is designed for large quantity poultry manure composting. It’s smallest composting width is 1.5m, the turning width is 8-30m. With it, you can get quality composting fertilizer easily, which can greatly improve the efficiency of your organic fertilizer factory.
2.Low energy consumption
To improve the efficiency of wheel compost turner, we choose SKF bearing pedestal–the best bearing pedestal in the world. Even though the wheel with several tons, a man can toggle it easily. That’s really an excellent way to reduce the energy consumption.
3.High automatic degree
We equipped PLC electric control cabinet for the composting machine. When working, it can be totally automated, you cost of ablor can be reduced very well. Because of the high speed running composting wheel, the fertilizer materials will be lifted. So you just need to build a deep groove with fertilizer conveying equipment beside the composting groove, the lifted composted fertilizer materials can move to next organic fertilizer making process.
4.Stable structure
We use 10mm thick square steel tube for the load-bearing bracket. That brings the machine more stable structure and longer service life than the traditional composting machine.
Poultry manure refers to all kinds of livestock waste and animal poops. They are the most common materials for making organic fertilizers. Then, what’s the procedure of making poultry manure into organic fertilizer? Next is the brief introduction.
- Using solid-liquid separator machine to reduce the moisture content of the raw materials.
- Add some auxiliary materials to the dewatered manures. Such as straw powders, sawdust, grass powder, etc. Then choosing a mixing machine to mix them evenly.
- Choose a moving type compost turner or crawler composting machine to make the fertilizer materials get better and fast fermenting.
- After composting, if there are stock materials, you can choosing a crushing machine to crush them into powders or small particles. The fertilizer crusher also can be used for crushing auxiliary materials.
- Make the pretreated materials into granules. As an experienced fertilizer machine seller, we have 6 kind of organic fertilizer granulator can be you choice. We can also recommend you the suitable one according to your capacity or raw material.
- Post-processes: Drying-Cooling-Screening-Packing.
If you want to get more details about making poultry manure organic fertilizer, welcome to: https://fertilizerplantequiment.com/organic-fertilizer-manufacturing-plant/
As we know, most of the raw materials for the production of organic fertilizer are agricultural wastes, such as livestock manure. So in the process of organic fertilizer production, if not handled properly, it will cause secondary pollution to the ecological environment. Therefore, the site selection, planning and design, raw material selection and process determination of organic fertilizer plant are very important. Then, how to solve these questions and start a reasonable organic fertilizer making project?
- Selection of raw materials. Before determining the raw materials of organic fertilizer factory, it’s very necessary to consider the quantity, nutrient content and price of raw materials, and whether the raw materials can be supplied continuously. If you have your own poultry farm, things will be much easier.
- Selection of the organic fertilizer factory site. At first, to minimize the pollution and bad influence when making organic fertilizer, you can choose to set up the plant far away from residential areas. It will be better if your factory is close to the origin of main raw materials, which can save you a lot of cost of transporting.
- Layout of the organic fertilizer plant. Reasonable layout can avoid the waste of space, and it’s also the guarantee of high efficiency. If you don’t have the experience of making layout, as a professional fertilizer equipment supplier, we can provide you free efficient layout, so just contact us.
With the development of fertilizer making industry, people make organic fertilizer or run compound fertilizer plants more easily. High automatic degree fertilizer machines also greatly improve the efficiency when making fertilizers. Fertilizer plant owners also cost less on hiring workers. So how much labor does a fertilizer plant cost with SX equipment? The following is some information about that.
Before calculating the labor you need when making fertilizer, it’s necessary to know which process of fertilizer plants need people to operate.
For organic fertilizer making plants, one person need to operate the windrow compost turners.
Next is packing. In fact, our packing machine also has high automatic degree. But it needs a person to operate the sewing parts when packing fertilizer products.
As for other processes, such as granulating, mixing, conveying, screening, etc, you don’t have to arrange operators. Almost all of our fertilizer machines are full automated. If you don’t know how to make sure the machines can run smoothly, we can make complete layout for you.
In a word, making organic fertilizer only takes at least two people. But it’s necessary to arrange one or two people to observe the fertilizer making process or maintain machines if something happens during machines working. So, with SX fertilizer equipment, you just need 3-4 operators for an organic fertilizer manufacture plant.
Organic fertilizer granulating machine is a kind of important equipment widely used for organic fertilizer production plants. But there are many points to pay attention to when using granulating equipment for the first time. If not, it’s very easy to reduce the granulator performance and even damage it. So what should be paid attention to when using a new organic fertilizer for the first time? Here are some details.
- All parts of the new organic fertilizer equipment have not been run in, which may cause jamming. So when the operatoruses the equipmentfor the first time, it is necessary to raise the temperature of the equipment so that the motor belt can be raised freely by hand. Then, the motor is connected and pulled according to the normal operation option for 8-10 times to gradually increase the temperature.
- In addition to the preliminary temperature regulation, the organic fertilizer granulator still needs to continue heating after starting up to replenish heat. At the same time, it should be adjusted to different temperatures according to different properties of materials.
- During normal operation, the temperature of the machine should be kept stable, and it should not be high or low. The temperature near the vent hole until the head part should be kept at about 200 degrees. At this temperature, most materials can be granulatedwell.
- During shutdown, the operator should completely cut off the power supply, and take down the parts with spanner on the head of the equipment, and wait for the next time to warm up separately.
Knowing about these matters, your organic fertilizer granulator can work efficiently and has a longer working life.
Crawler type fertilizer turning machine is a kind of high efficiency windrow compost turner. It can be used for all kinds of organic fertilizer making plants. For making sure its high performance, the maintenance is very important:
- Before running the crawler type composting machine, you need to check whether the parts are normal.
- When the machine is working, especially around high-speed parts, it’s strictly forbidden to stand around the equipment.
- If there is abnormal sound during working, you should stop the machine immediately for inspection. It is confirmed that there is no fault before continuing to work.
- If you want to check the composting teeth, transmission shaft or other parts, the machine must stop working. If you want to replace machine parts, the power must be cut off. It’s strictly forbidden to change parts when the engine is not off.
- After composting, the winding materials and hardened attachments on the turnover shaft should be removed. And it’s better to check main parts of the machine, such as the composting teeth, circuit facilities, conveyor belt and crawler tightness. If there are something wrong, you can repair the machine in time to prevent the next use.
ShunXin fermentation pot can be used for all kinds of poultry manure fast composting. For composting chicken manures, you can collect them together and add some fermenting bacteria, then put them into the fermentation pot. The composted chicken dungs can be used directly for crops, plants or granulating. After a brief understanding of chicken manure fermentation pot, what are the advantages of it? Next, you may get more information.
Small floor place: Adopts vertical structure design, the fermentation pot has high working efficiency but only covers a little space. Because of the machine is sealed, you can also use it outdoors.
Considerable economic benefits: It can compost 5-150m³ chicken manures per time(we can customize the machine according to your capacity requirement), which can greatly improve your organic fertilizer factory efficiency and bring you adorable profits.
Good environmental benefits: The sealed design can greatly improve fermenting temperature in the pot, which can kill pest eggs and grass seeds efficiently. After composting, the manures will not release bad smells. That will greatly reduce air pollution.
High fermentation maturity: If you make the organic manures ferment naturally, the whole process may take very long time, even several months. Using fermentation pot, the composting of chicken manure only takes you 7 days. High performance makes it possible to work whole year and not affected by the weather.
To make sure the organic fertilizer drying machine run smoothly and normally, the fan system can’t be ignored. There are some things you need to focus on when using fertilizer drying machine:
- Frequently observe the operation of the fan. If the flow rate is too large and does not meet the requirements, or a small flow rate is required in a short time, you can use the throttling device for adjustment.
- Regularly check the sensitivity of thermometer and oil gauge, and control the oil tank level of bearing within the specified range.
- Check the bearing base regularly, clean and add lubricating oil to prevent the bearing from burning out.
- If there is any abnormal phenomenon during the start-up, shutdown or operation of the organic fertilizer dryer fan, you should check it immediately.
- For the faults found in the inspection, find out the causes and eliminate or deal with them immediately. If they can not be eliminated or major faults are found, they should be stopped immediately for maintenance.
When making organic fertilizers, if the raw material particles are too large, it will not only affect water regulation, but also affect the mixing uniformity of materials.
Especially for some materials with large lumps or high cellulose content, such the composting of horse manure, if they are not broken to a certain extent, they will slow down the microbial decomposition rate.
Such as the common cow dung and straw compost. If the straw is not crushed before composting, even in summer, the whole composting process will cost two months; if the straw is crushed into 10 cm pieces, it will be completely decomposed in less than one month; if the rice straw is ground into 3 ~ 5mm straw powder, the complete decomposition time is only 10 ~ 15 days.
For faster composting of organic fertilizer materials, you can choose compost turning machines. They can compost the fertilizer materials in only one week.
As we all know, it’s bad for the fertilizer efficiency if the fertilizer products are easy to cake. And why it always happens? As a professional organic fertilizer equipment supplier, we find these reasons may be useful.
- The production process of organic fertilizer always is unsealed. So when you making fertilizers, the higher the air moisture content is, the easier the fertilizer materials will absorb moisture and agglomerate. High air moisture content will also make the fertilizer products caking. So it’s better to make fertilizer in dry weather or store the products in dry places. You can also choose a dewatering machine for fertilizer materials and a fertilizer drying machine for fertilizer products.
- For compound fertilizers, there are different chemical fertilizer crystals in the products. If the room temperature and air moisture is high, the compound fertilizer granules is very easy to agglomerate. If you have compound fertilizer production line, dry granulating machine is the best choice for you. The storage of compound fertilizer granules also needs to be a dry environment.
- Another reason of fertilizer caking is the storage time. The agglomeration will happen easier when storage time is longer. Long time storage will also affect fertilizer efficiency. If you can’t run out the fertilizers in short time or you want to sell fertilizers, you can choose our fertilizer packing machines. They can help you store the fertilizer products easily and make it easy to sell them.
- Reduce environmental pollution
With the help of organic fertilizer production equipment, manures from animal farms can be removed at any time. Fresh animal waste is treated by a series of organic fertilizer production equipment, such as composting machine, semi- wet material crusher, mixing machine, fertilizer dryer, etc.
Firstly, the treated manure is to remove the odor; the second is to completely kill all kinds of pathogenic bacteria, insect eggs, grass seeds, etc.; the third is to remove harmful substances and avian influenza viruses. In this way, the maximum reduction of air pollution and environmental transmission damage and loss.
- Full development and utilization of resources
Since the organic fertilizer production equipment, a large number of livestock and poultry manure has become a huge and valuable wealth, scientific development and utilization make it into a treasure. It is a good raw material in the production of organic fertilizer, and also brings certain economic benefits to farmers.
- Increase economic benefits
Now more and more people use organic fertilizer, and the market of organic fertilizer is very good. Choosing our organic fertilizer equipment, you can get high quality organic fertilizer, which can bring you considerable profits.
Before making organic fertilizer, the pretreatment of raw materials is needed, and these machines may be helpful:
1. Screening Machine
For some organic fertilizer factory which uses industry organic waste as their materials(such as mushrooms, filter mud and biogas residue), it’s better to screen out the extra materials before making them into organic fertilizer. With rotating fertilizer screener, you can make fertilizer more efficiently.
2. Crushing Equipment
Some organic fertilizer raw or auxiliary materials can’t be composted directly because of long or large shape. To solve this problem, you can choose a fertilizer crushing machine, such as semi-wet crusher, cage crusher and so on. They can crush materials into small particles, which can help your fertilizer plant run more smoothly.
3. Dewatering Machine
Dewatering machine is mainly suitable for poultry manures and animal wastes. Manures always have high moisture content, it’s obvious that they are not suitable to be directly made into fertilizer. By using solid-liquid separator machine, the moisture content of animal manures can be reduced to about 30%, which is the appropriate value for making organic fertilizer.
In the production process of organic fertilizer, the construction of ventilation system is very important. By controlling the ventilation rate, the system temperature can be adjusted, the suitable environment for the growth and metabolism of microorganisms can be provided. Therefore, ventilation in composting is necessary. During composting, ventilation has three main purposes: oxygen supply, dehumidification and cooling.
- Oxygen demand: the composting process is completed by providing oxygen for the growth, reproduction and metabolic activities of aerobic microorganisms.
- Dehumidification demand: ventilation can remove the moisture in the wet raw materials at higher temperature. When the air is heated by the composting substrate, the moisture can be evaporated and the compost materials can be dried.
- Cooling demand: ventilation can remove the heat generated by organic matter decomposition to control the process temperature.
The ventilation rate for oxygen supply mainly depends on the content of organic matter in composting raw materials, the proportion of degradable components in organic matter and degradable coefficient, which can be calculated by the chemical composition and degradation degree of organic matter in compost.
- Material selection is the core. When selecting materials, pay attention to the hardness of materials. The harder the material is, the more difficult it is to crush, and the more serious the damage to the crushing equipment will be.
- When the moisture content in the material is large, the material is easy to adhere in the mill, and it is also easy to block in the process of feeding and conveying, resulting in the reduction of crushing capacity. Therefore, to reduce the moisture content before crushing, so as to facilitate the pulverizer to work better.
- The more fine powder contained in the material before grinding, the more influence the crushing. As the fine powder is easy to adhere, the material with more fine powder should be screened earlier.
- The better the wear resistance of crushing equipment parts is, the greater the crushing capacity is. If it is not resistant to wear, it will damage the crushing ability.
Determine what machine you want.
The first thing you need to do for purchasing an ideal granulating machine is determine the machine you need. Suitable granulator not only can work well for your fertilizer making plant, but also can help you adjust your budget.
Pay more attention to quality, not just the price.
Some fertilizer equipment supplier may recommend you very cheap fertilizer machines. You may be attracted, but whether you consider its quality or not? Purchasing fertilizer equipment is not like buying clothes, you need to consider its quality, performance and efficiency.
Choose a reliable equipment supplier.
A reliable fertilizer machine manufacturer can provide you efficient equipment with affordable price and considerate service. Choosing this kind of supplier can help you make fertilizer granules much more easily with lower cost.
1.Causes soil salinization
If chicken manure is used for years, a large amount of sodium chloride remains in the soil. Too much salt will seriously restrict the permeability and activity of the soil. The solidification of important elements such as phosphate fertilizer, potassium fertilizer, calcium, magnesium, zinc, iron, boron and manganese restricts the improvement of crop yield and quality.
2.Burning roots and seedlings
It is easy to cause plant disease and death if chicken manure is not thoroughly fermented. If you insert your hand into the soil after using the chicken manure which is not thoroughly fermented, you will feel the soil temperature is higher. This is the second fermentation of raw manure in the soil. Especially in spring and summer, when the temperature is high in the greenhouse, the secondary fermentation of raw manure will emit a lot of heat, which is easy to cause root burning
3.Bring in antibiotics
Nowadays, in large-scale livestock and poultry breeding, a large number of antibiotics are used to improve feed utilization and promote animal growth. About 70% of antibiotics can not be absorbed after use, so the content of antibiotics in animal feces is generally high. The antibiotics contained in unrolled chicken manure will seriously affect the physiological process of crop roots and significantly inhibit its growth.
4.Breeding of root knot nematodes
Chicken manure is the camp and hotbed of root knot nematodes. The number of eggs carried by chicken manure is 100 per 1000 grams. The nematodes are extremely sensitive to chemical agents. After spraying, the nematodes will quickly move to the depth of 50 cm-1.5 m underground to escape. The nematode eggs in chicken manure are easy to hatch and multiply by tens of thousands overnight, so it is difficult to eradicate the disease.
- The special requirements of composting technology are realized, such as crushing raw materials, realizing quantitative displacement of raw materials or giving certain shape to raw materials pile.
- Improve the permeability of the raw material pile: the turning system can process the material into small lumps, making the material pile fluffy and forming appropriate porosity.
- Mixing function in raw material conditioning: in fertilizer making, some auxiliary materials need to be added in order to adjust the carbon nitrogen ratio, water content and pH value of raw materials. The agitator can be used to mix the main raw materials roughly stacked together according to the proportion with various auxiliary materials, so as to achieve the purpose of quenching and tempering.
- Adjust the moisture content of raw material pile: the suitable moisture content of raw material fermentation is about 55%, and the moisture standard of finished organic fertilizer is below 20%. The forced steam emission will be formed when the material is turned by thecomposting machine, which can reduce the water content and improve the fertilizer production efficiency.
- Adjust the temperature of the raw material windrow: during the operation of the compost turner, the raw material pellets and air are fully contacted and mixed. When a large amount of fresh air is kept in the windrow, the aerobic microorganisms will become active, thus producing fermentation heat and increasing the stack temperature; when the temperature is high, fresh air can be added to reduce the stack temperature. The formation of medium temperature to high temperature and then to medium temperature to high temperature, such a cycle state, all kinds of beneficial microorganisms grow and reproduce in their adaptive temperature range.
The quality of fertilizer turning equipment can be analyzed from the aspects of its materials and treatment effect. If it is a high-quality compost turner, its structure will be more perfect, the internal use of stainless steel material, strong corrosion resistance, long service life; if it is a shoddy manufacturing equipment, then as a professional, it can be judged from its external contour.
Moreover, the high-quality turner not only has high degree of automation, less energy consumption in the treatment process, but also adopts biological deodorization, which will not produce secondary pollution in the treatment process. It is equipped with auxiliary air supply heating device, which can operate normally even in low temperature environment.
After determining the quality of the composting equipment, it is particularly important to note that before formal use, it is necessary to understand some basic conditions for the operation of the process. For example, the ambient temperature should be maintained between 50 ℃ and 65 ℃ as much as possible, and the time to maintain above 55 ℃ should be more than 5 days.
In addition, the organic matter content should be greater than 20%, the moisture content should be maintained between 50% and 65%, and the ph value should be controlled between 7 and 8.5. After knowing these equipment parameters, I believe it will be helpful to your purchase.
1.Maturity of fermentation:
Appearance change: the visual qualitative judgment standard is that the fermentation will not undergo fierce decomposition, the product temperature is lower, the appearance is tea brown or black, and the structure is loose without odor;
Temperature change: after the high temperature stage, the temperature of the compost will gradually decrease. When the fermentation reaches maturity, the temperature of the fertilizer is basically consistent with the normal temperature.
2.Chemical index:
Changes of organic matter and volatile solid content: with the progress of fermentation, the content of organic matter and volatile solid showed a continuous downward trend, and finally reached the basic stability. When it reaches maturity, it can decrease by 15-30%. However, this trend is greatly affected by the source of raw materials. It is not enough to judge whether the fermentation is rotten or not.
The change of C / N ratio and inorganic nitrogen forms: during the fermentation process, part of organic carbon will be oxidized to carbon dioxide, volatilization loss, and the mass of compost pile will be reduced. Some studies have shown that when the C / N ratio of compost decreases from 25-35:1 to below 20:1, the compost will be stable.
Ratio of water-soluble organic carbon to organic nitrogen: the ratio of water-soluble organic carbon to water-soluble organic nitrogen is a good chemical indicator of fermentation maturity. When the value is about 5-6, it indicates that the fermentation has been decomposed, and this value has nothing to do with the fermentation raw materials.
- Machine and base resonance
Cause: in the production of rotary drum organic fertilizer dryer, due to the strong rotation of the equipment, it will produce a certain amount of resonance effect with the base, which is very harmful to the equipment and will also affect the working effect.
Solution: at first, in the construction of the base, it should be poured with cement and added with anti vibration wood bed. Second, in production, pay attention to the actual capacity of the machine, not to overload the machine.
- Material blocking at outlet
Reason: the material with more moisture is easy to form block, and the material outlet will be blocked when it reaches the outlet of organic fertilizer dryer.
Solution: in addition to strictly controlling the process formula, when the particle size of the material entering the organic fertilizer dryer is large, the relevant personnel should be informed in time to pay attention to the discharge at the tail of the machine, so as to prevent the bag film and bag line from entering the production system.
- The meshing clearance between the big gear and the small gear is damaged
Causes: tugboat wear, block wheel wear, pinion wear.
Solution: remove or replace according to wear condition, or install on the opposite side or update in pairs.
Working principle of self-moving manure turner: diesel engine is used as power source, working through power transmission system, materials are rotated by composting teeth, and composting fermentation of fertilizer is controlled by personnel driving.
Features of moving type compost turner:
- It is more suitable for the mechanism and process requirements of microbial fermentation of poultry manure. It can effectively mix the sticky poultry manure, microbial preparation and straw powder. It creates a better aerobic environment for material fermentation.
- According to the technical parameters of the machine, the machine can turn 400-500 cubic meters of fresh poultry manure per hour. The whole production line needs 4 or 5 personnel at most. The price advantage of finished fertilizer is obvious.
- The overall structure of this kind of turning machine is reasonable, the whole machine has good rigidity, balanced force, safe and reliable performance, easy to operate and strong applicability to different sites. All parts are standard parts, easy to use and maintain.
- Advanced fermentation technology. According to the principle of aerobic fermentation, the fermentation bacteria have the space to give full play to its functions.
Because of all operations and equipment operation in granulating process are carried out around organic fertilizer granulation, so organic fertilizer granulator occupies an important position in the whole organic fertilizer production process.
The quality of granulation also affects the shelf life and the degree of going out of the organic fertilizer granules, thus affecting the sales price.
Maintenance method of organic fertilizer granulator:
- Keep the working site clean and prevent the dust and sundries from entering the granulator and affecting the work.
- Check the lubrication condition of all working parts and use lubricating oil in time to ensure the normal operation of the machine.
- Always pay attention to the operation of organic fertilizer equipment. If abnormal sound is found, it should be stopped immediately and checked. After troubleshooting, it can be used. If the corresponding reason is not found, the machine can not be started.
- When the organic fertilizer equipment is overhauled, the working clearance should be re measured each time and adjusted, and it can be continued to use after meeting the standard.
- If the organic fertilizer equipment can not operate by pressing the program controller, check whether the power supply voltage, power plug socket and connecting plug socket are normal, and check the internal fault of the controller.
Working Process:
- Put the raw materials into the composting groove.
- Raw materials are stirred to the outlet by the equipment every day, and the traveling distance is same.
- After 30 days of fermentation, the raw materials will be completely composted and converted into organic fertilizer.
- After a period of aerobic fermentation, the finished organic fertilizer can be obtained from the outlet every day, and the cyclic fermentation of fertilizer can be formed.
Tip: Adding a certain amount of organic fertilizer starter before fermentation can greatly shorten the fermentation time of raw materials, improve the fermentation efficiency, make the fermented organic fertilizer contain more organic matter and improve the utilization rate of organic fertilizer.
Characteristics:
- With high efficiencyand stable operation, it can compost different materials evenly and consumes low energy.
- Centralized control of control cabinet can realize manual or automatic control function.
- Equipped with soft starter, the impact load is low when starting.
- The composting teeth are firm and durable, and has certain crushing and mixing functions for materials.
- Limit travel switch for safety and limit operation.
In order to ensure its service life, timely maintenance and care should be taken in the process of operation.
To help you make fertilizer granules more efficiently, we always provide you considerate customized service:
Parts of different granulator: when granulating, especially using rotating granulators, the temperature would greatly improve, which would fasten the evaporation of raw material moisture. So if you have the needing of keeping moisture, we can equip a spray system for you. It can spray water to the materials when granulating, greatly improve the quality of fertilizer granules. For double roller granulator, we can customize the shape and size of the ball socket of the roller sheet for you.
Capacity: we can making different capacity granulators, they can meet your need of starting small, medium and large organic fertilizer making plant. The price is also very reasonable.
Other aspects: we can design the height of the granulator according to your fertilizer plant layout. That will make sure the fluency of your fertilizer plant and improve the granulating rate. Even the color of the granulator can also be customized if you want.
ShunXin has more than 15 years of domestic and foreign trade experience. That helps us form a complete service system.
Pre-sale service: With 15 minutes after receiving your information, we will timely contact you and provide you professional service including product inquiry, technical support, product service complaint, warranty, consultation of spare parts and so on.
Free project design and installation guidance: If you don’t have the experience of starting fertilizer factory, we can provide you free layout according to your information. We can also arrange professional technician to guide you how to install and use the machines.
Customized service: Considering that some customers may have special need of our equipment, we launched customized service. We can customize the machine based on your demand, such as the capacity, powder, some auxiliary parts and the appearance of the machine. These are all for you to get the ideal machine.
After-sales service: After your machine is put into operation, we will follow up and visit irregularly to check the machine operation, production capacity, service condition of wearing parts and other problems you get when producing fertilizers, so as to solve the problems immediately and give you more technical guidance.
There are three forms of organic fertilizer you can make: composting fertilizer, powder fertilizer and granular fertilizer.
Making composting fertilizer doesn’t need many steps. You just need to build composting groove or pile raw materials into long windrows. Then choosing appropriate organic fertilizer turning equipment to help materials get better fermenting. After composting, you can use the products for your plants.
If you want to get powder fertilizer, you can use a fertilizer crushing machine, it can crush the organic fertilizer materials into even powders with small particles.
Making granular fertilizer is the finish processing of powder fertilizer and composting fertilizer. With a granulating machine, you will get wonderful organic fertilizer pellets.
A whole composting process contains 4 necessary stages:
- Heating stage. In the early stage of composting, the microorganisms in composting are mainly mesophilic and aerobic. They start the fermentation process of composting, and decompose organic substances (such as simple sugars, starch, protein, etc.) under aerobic conditions, and generate a lot of heat. The composting temperature is continuously increased from 20℃ to 40℃.
- High temperature stage. With the increase of temperature, the thermophilic microorganism gradually replaced the medium temperature type and played a leading role. The temperature continued to rise, reaching above 50℃in a few days, and entered the high temperature stage.
- Cooling stage. When the high temperature stage lasted for a certain period of time, most of cellulose, hemicellulose and pectin had been decomposed, and the complex components which were difficult to decompose and the newly formed humus were left. The microbial activity was weakened and the temperature gradually decreased. When the temperature drops below 40℃, mesophilic microorganisms become the dominant species.
- Maturity stage. After composting, the volume of compost is reduced, and the temperature of compost decreases to a little higher than the air temperature. At this time, the compost should be compacted to cause anaerobic state and weaken the mineralization of organic matter, so as to maintain the compost.
- Control the quality of powder fertilizer materials.
Strictly control the quality of powdery raw materials according to the formula of making organic fertilizer granules. Good quality fertilizer materials makes the granules making process more efficient. If there are too much extra materials in powder fertilizer, the quality and granulating rate will be affected.
- Control the moisture content of powder fertilizer.
The suitable moisture content of raw materials is about 30%. If the moisture is too high, they would stick together. If the moisture is too high, they may not have enough cohesion to become fertilizer granules.
- Choosing reliable disk granulator supplier
A reliable fertilizer machine manufacture must can provide you high performance equipment. That’s also the basis for increasing the granulating rate. Take ShunXin disk granulator as an example, we design scraper and spray system for the pan granulator. They are used for reduce the fertilizer sticking on the disk and keep the moisture content of fertilizer materials.
- Improving the technical level of operator.
Operating is the key to produce quality fertilizer granules. It is very important to strengthen the training of operators’ skill level. Or you can hire experienced workers.
Composting is a process in which the manure collected in the fecal canal of the farm is dehydrated by a solid-liquid separator, and then mixed with some auxiliary materials to adjust the carbon nitrogen ratio. Through the up and down tossing of the composting machine, aerobic fermentation is carried out to form organic fertilizer and soil amendment, so as to achieve the purpose of harmless, reduction and resource utilization.
The emergence of the compost turning equipment is gradually replacing manual material turning. It has the following functions in composting.
- The special requirements of composting technology are realized, such as crushing raw materials, realizing quantitative displacement of raw materials or giving certain shape to raw materials windrow.
- Improve the permeability of raw material windrow: the turning system can process the materials into small lumps, and make the thick, elastic and dense raw material windrowbecome fluffy and form appropriate porosity.
- Mixing function in raw material conditioning: in fertilizer making process, some auxiliary materials need to be added in order to adjust the carbon nitrogen ratio, water content and ph value of raw materials. The agitator can be used to mix the main raw materials roughly stacked together according to the proportion with various auxiliary materials, so as to achieve the purpose of quenching and tempering.
As an efficient organic fertilizer granulating machine, the pelletizing rate of rotating drum granulator can reach 90%, and the it’s easy to operate and maintain. The specific advantages are as follows:
1. Increase the material temperature during the operation of the drum granulator, so that the moisture content of the material after pelletizing is low and the drying efficiency is improved.
2. The drum granulator is lined with rubber engineering plastics, so the raw materials are not easy to stick to the cylinder, and have the function of anti-corrosion and heat preservation.
3. Ultra high molecular weight polyethylene is used to build the inner lining of granulator equipment, which eliminates the phenomenon of material sticking to the wall and reduces the labor intensity of workers.
4. The drum granulator has large capacity, low power consumption, low maintenance cost and long service life.
ShunXin rotary drum granulating machine has great efficiency and quality, choosing it, you will make fertilizer much easier.
Organic fertilizer materials always are some animal wastes or livestock manures. These materials always have bad smells, which are bad to environment and people’s health. So how to solve the odor? You may get the solution from the following content.
- Make a good formula of raw materials and keep the raw materials mixed well. Before composting, the livestock manures always need to be mixed with some auxiliary materials. Mixing them evenly can partly reduce the bad smells of manures.
- Store raw materials as quickly as possible. If you don’t collect and store the raw materials in time, the materials may compost naturally, produce bad smells. The fertilizer efficiency also will be reduced.
- Keep the moisture content of materials about 30%.
- Ensure the air permeability of raw materials. If the materials can’t contact enough air, the anaerobic fermentation will occurs, which will cause serious bad smeels.
- Make sure the composting site is flat ground, prevention of puddles and ponding.
- Keep the composting machine clean and dry.
In the working process of organic fertilizer granulating machine, it is required that the material has a certain viscosity. Some raw materials are loose after fermentation, and it is not easy to granulation. If it is not easy to granulation, some water or adhesive should be added to increase the viscosity of the material. Organic fertilizer equipment pan granulator and rotary granulator are granulated by pellet method. Water or binder will be added in the process of granulation to ensure the smooth granulation of materials. The new organic fertilizer granulator adopts wet granulation method, and the material after fermentation can be directly granulated, without the operation of other processes.
If the moisture content of the material is too high, you can add some dry materials to neutralize the moisture content. If the water content is too low, it is easy to granulation.
Before granulation, there is no need to stop the processing, crushing and composting of raw materials, which can directly realize the batching processing and direct granulation, which not only saves a small amount of power input, but also effectively reduces the cost, and also realizes the greater improvement of task efficiency, which is convenient and fast, and the effect is satisfactory. The new type of organic fertilizer wet granulator also achieves 100% organic content, realizing the exclusive manufacture of pure organic fertilizer.
To get more profits from organic fertilizers, the best way is to improve the nutrient purity. There are two suggestions:
Roughing of raw materials–screening
The raw materials of organic fertilizer are always some animal manures, industry wastes, sludge and so on. There are many useless materials, which are not suitable to be fertilizer, but also harmful. To pick them out, you can choose screening machine. This equipment can screen out the redundant matters from the raw materials. After screening, the quality of fertilizer can be partly improved.
Fine finishing–composting
This is the deep processing of screened materials, and it’s mainly suitable for composting animals waste. With the help of composting equipment, manures can get fine fermenting. Because of the high temperature when composting, the plant weeds, pest eggs and other harmful materials can be greatly destroyed. As a result, the fertilizer products have better quality and competitiveness.
Before knowing how to reduce the moisture of animal manures, we should know why they need to be dewatered.Whether you want to compost the manures or make them into organic fertilizer grnaules, the high moisture will be the hinder. It will cause many questions, such as the loss of fertilizer nutrient, air pollution, bad smells and breeding of flies.
So how to dispose animal manures to suitable moisture?
The traditional way is to dewater them naturally. That will cost a lot of time, prolong the process of making fertilizer. To shorten the timing consuming and improve your efficient of making organic fertilizer products, we designed two types of high performance solid-liquid separator machine: screw extrusion type and inclined sieve. They have great capacity and high automation for dewatering animal manures. Using them, you would make fertilizers more smoothly.
Which materials are suitable for dry granulation method?
Fertilizer materials with about 10% moisture can be regarded as dry materials. Dry granulation method is the way to make dry fertilizer materials into granules. So no matter you want to make organic fertilizer or compound fertilizer, the dry granulation method is suitable.
What machines are used for dry granulation?
In ShunXin, there are two kinds of dry granulation equipment: double roller granulator and flat die granulating machine. The first one makes fertilizer granules by the extruding of two rollers. The second one works by the extruding of roller and granulating mold. The most convenience of these two granulators is that you don’t need to dry the final granules, that will save you the cost of drying machine. And no matter which one you choose, all of them can work well for your fertilizer making plant.
Chicken manure is always the efficient fertilizer materials for plants. But if you fertilize chicken to plants directly may cause some problems. To make better use of chicken manures, there are two main ways for choosing.
The first is simply treatment–composting. You can use compost turners to help them ferment. That will destroy the useless materials in chicken dungs, such as pest eggs, grass weeds and some harmful matters.
The second is fine machining–granulating. That means granulate chicken manures into pellets. Using this way, you will get great chicken manure fertilizer granules. You can use it for your own plants or you can pack them into bags for sale. No matter using or selling, this way is really recommended.
1. Dewatering
Poultry manures have high moisture content, which will affect the granulating process of them. Therefore the dewatering of animal manure by solid-liquid separator machine is very necessary.
2. Composting
Poultry animals always don’t have good digestive capacity. So there are some useless materials in their manures, such as pest eggs and plant weeds. And they ferment naturally costs long time. In case to solve these problems, you need to compost them in advance.
3. Granulation method
Manures with about 10% moisture content are suitable for dry granulation equipment; 10%-30% moisture manures need wet granulation equipment.
4. Drying
Using wet granulation machines, the final fertilizer granules need to dry. To shorten the time consuming, you can choose our fertilizer drying machine.
Composting refers to the process of helping animal manures get better fermenting by compost turners. It’s an important step in organic fertilizer manufacturing plant.
As the efficient materials of making organic fertilizer, animal manures always need to be composted before being fertilizer products. The composted materials will have higher purity of nutrients. To make quality composting fertilizer, high performance compost turning equipment is very necessary. They can compost windrow manures or work in ferment grooves. Using them, time consuming for manures fermenting can be shortened greatly, useless matters such as pest eggs, plant seeds and bad smells, can be completely wiped out.
As for rotating types fertilizer granulators, you can adjust the rotating speed of the rotor. Want large fertilizer granules, you can set the rotor with low rotating speed. On the contrary, want small fertilizer pellets, you just need to fasten the rotating speed of the rotor.
For adjusting the size of fertilizer balls produced by disk granulator, you just need to adjust the inclination angle of the pelleting disc.
Refer to extruding granulator, the extrusion force can be adjusted by hydraulic system. Small extruding pressure brings large holes, the pellets will be large. Large extruding pressure brings small holes and granules.